Supplier Plant Visit at the World’s Largest Volvo Truck Manufacturing Facility, Part 1
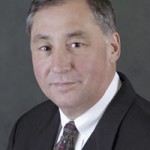
Robert Menard,
Certified Purchasing Professional,
Certified Professional Purchasing Consultant, Certified Green Purchasing Professional, Certified Professional Purchasing Manager
Editor’s note: By profession and providence, I have learned and absorbed so much knowledge from the many visits to all sorts of production and service facilities around the world over many years. Since the early 1990s, I have marveled at metal forming machines in Taiwan, glass fabricating machines in Italy, plastic extrusion equipment in the US, and mining apparatus in Argentina, that could do everything but talk to you. How quaint a memory; today they not only talk to you, but anticipate your questions. This is the first part of a three part story about my visit to the Volvo plant in Virginia.
Sometimes you just get lucky!
Good fortune found me in Dublin, VA when the opportunity arose to visit the Volvo Group Trucks Operations Americas Cab & Vehicle Assembly New River Valley (NRV) Plant . A friend in western VA, where NRV is located, knows that logistics and transportation clients were a substantial part of my consulting practice. We had discussed the essential requirement of supplier plant visits as the lynchpin to successful supplier qualification , supplier evaluation , partnering , and Merger & Acquisition activities so this favor represented a major tour de force for me. To sum up my experience in one short word, WOW.
The bird’s eye view
This plant assembles the heavy duty trucks seen everywhere on our streets and highways. They haul freight in trailers and containers. These trucks are known as semi-trailers or “tractors” in the US. When attached to a trailer, the truck-trailer unit is affectionately known as the “18 wheeler”. Many trucking industries and associations have adopted and co-opted the slogan, “America moves by truck”. Well, many logistics firms would argue about this but let’s go with it for our purposes.
The tour
The VP of HR Volvo Group Trucks America escorted a group of six on a 3 hour tour. We began with the Special Vehicles sub-plant which produces far fewer but more specialized units per day. Our host must have been trying to ease us into the awe of we would see next, the full glory of the computerized assembly flow of the main production facility.
Others in the group of six gawking visitors were not manufacturing or supply chain pros so their fascination was limited to seeing mechanized and assembly flow processes for the first time. The plant assembly lines are intensively high-tech managed with automated vehicle guidance systems (AVGS), cartage apparatus and automated storage and retrieval systems, ASRS, and for pre-painted cab sub-assemblies using Radio Frequency Identification (RFID).
The ASRS was a real hoot. A fully automated “virtual robot” continually receives commands generated from the automated assembly line for pre-pained and pre-assembled cab and chassis units stored in a tower warehouse. It was so cool to see the unmanned vehicle racing at super human speed (no kidding) using RFID to locate and retrieve the stored cab and chassis units and then escort them to the assembly line for further manufacture.
Technical choreography
In the hands of a pro, excellence looks easy. Wayne Gretzky, the Great One, made exceling at hockey look like child’s play. Jay Leno is a master of comedy, Robert De Niro is an acting talent beyond peer, Bill Gates is a paragon of business and so forth. In every walk of life, successful people make it look easy
The untrained eye might see the ideal smooth flow but not appreciate the genus behind making it look easy. This plant just does not proceed on autopilot. The timing and logical order of operations is overseen in a computerized control room. I have seen these at clients like NASA headquarters, BNSF Railway offices in Fort Worth, and dozens of cement, steel, glass, and other manufacturing facilities around the globe.
Despite all the high tech wizardry and programmed efficiency behind this split second production timing, any employee can stop the production line should any life safety issues arise. This is the chevron of a company focused on its human capital, a quality oft claimed but rarely earned.
Quick stats about the plant
- · Average daily production of two shifts
- o 110 standard units
- o 16 special units
- · Located on 293 acres bordering Interstate 81 in Dublin, VA
- 4881 Cougar Trail Road, P.O. Box 1126, Dublin, VA, 24084
- · Constructed in 1974 by White Motor Co., it was acquired by Volvo in 1981
- · The NRV comprises 1.6 million square feet, or more than 35 acres under roof
- · A total of 87 robots are used in the cab and paint facilities
- · More than 2,000 people currently work in the plant.
- · Certifications
- o ISO 9001 quality
- o ISO 14001 environment
- o ISO 5001 Energy
- o Virginia Governor’s Environmental Excellence Award
- · NRV reduced its energy intensity by nearly 30 percent in just one year